Unlocking the Potential of **Precision Molds** in Metal Fabrication
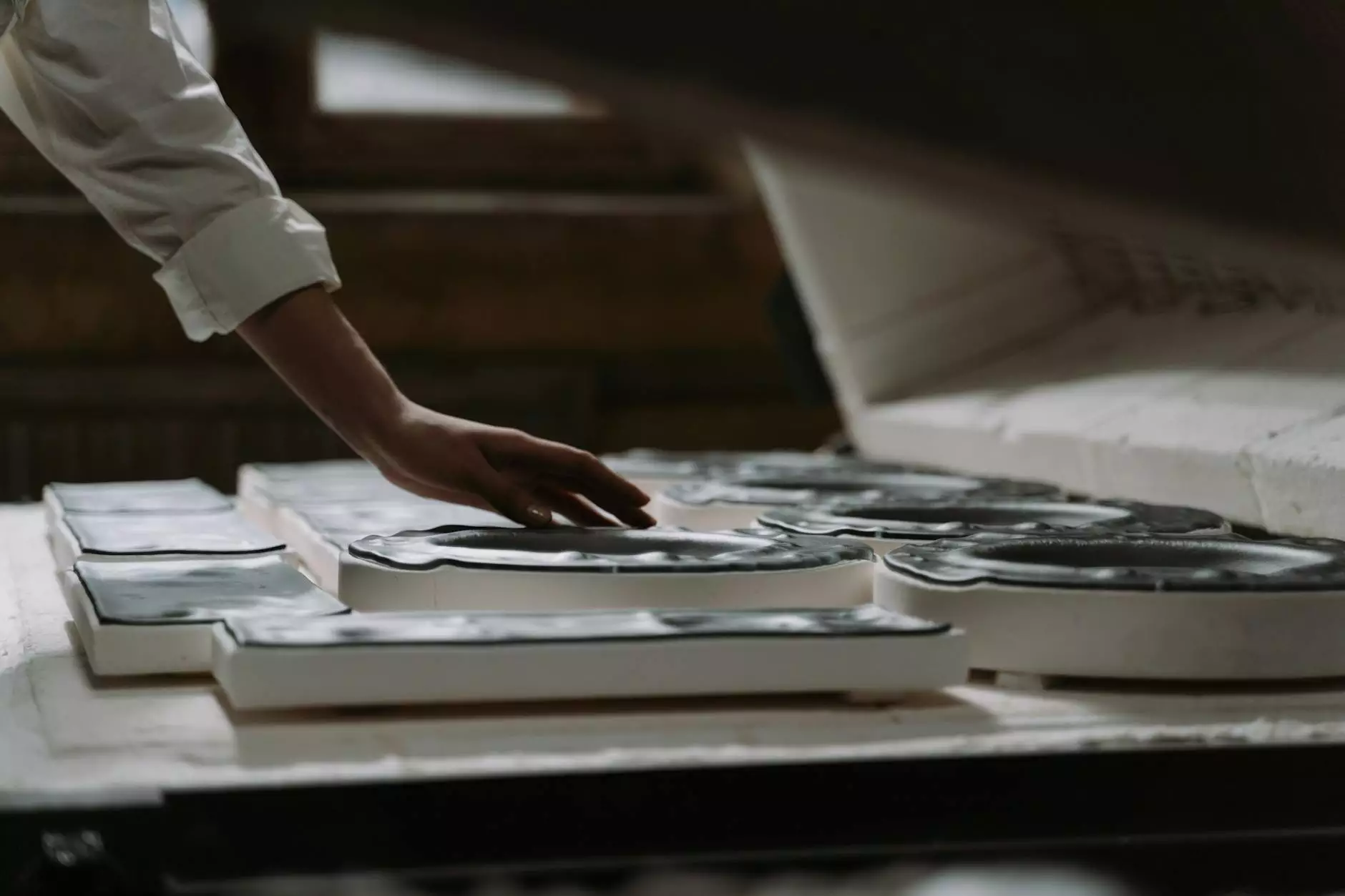
In the competitive landscape of manufacturing, leveraging the most advanced techniques and tools is crucial for success. Precision molds play a pivotal role in enhancing the quality and efficiency of production in the metal fabrication industry. This article delves deep into the world of precision molds, exploring their benefits, applications, and how they can significantly impact your business on deepmould.net.
What are Precision Molds?
At its core, a precision mold is a high-accuracy tool used in the manufacturing process to shape and form materials, particularly metals. These molds are crafted to extremely tight tolerances, ensuring that each piece produced is consistent in dimensions and quality. The use of precision molds is essential in industries such as automotive, aerospace, electronics, and medical devices, where the integrity of each component is paramount.
The Importance of Precision in Manufacturing
In today's fast-paced manufacturing environment, the need for precision cannot be overstated. Here are several reasons why precision is critical:
- Quality Assurance: Precision molds ensure that every product meets strict quality standards, minimizing defects and rework.
- Cost Efficiency: By reducing waste and the need for revisions, precision molds can lower overall production costs.
- Time Savings: Faster production times can be achieved with the use of high-quality molds, speeding up time-to-market.
- Customer Satisfaction: Consistent product quality leads to higher customer satisfaction and repeat business.
Applications of Precision Molds in Metal Fabrication
Precision molds find a wide array of applications within the metal fabrication sector. Here are some notable examples:
1. Automotive Industry
The automotive industry demands high precision for safety and performance. Precision molds are used to create:
- Panels
- Engine components
- Transmission parts
- Electrical connectors
These molds ensure that all components fit together seamlessly and function correctly.
2. Aerospace Sector
Aerospace components often endure extreme conditions, making precision vital. Precision molds are used to manufacture:
- Flight control surfaces
- Engine housings
- Landing gear components
The integrity of these components directly affects flight safety, which is why precision must be upheld.
3. Electronics Manufacturing
With the rapid growth in technology, electronics manufacturing relies heavily on precision molds for:
- Casings
- Heat sinks
- Connectors
High precision ensures compatibility and performance of electronic devices.
Advantages of Using Precision Molds
The integration of precision molds into your manufacturing process can bring numerous benefits. Let’s explore the advantages in detail:
Enhanced Product Quality
By using precision molds, manufacturers can achieve a higher quality of finished products. Each mold is designed to reproduce components with exact shapes and dimensions, ensuring that every piece meets the required specifications. This leads to fewer defects and quality variances, further enhancing the overall reliability of the product.
Increased Production Rates
With precision molds, manufacturers can streamline their production processes. These molds can be designed for quick changeovers, allowing for increased uptime and more efficient production schedules. This results in faster output without compromising quality.
Reduced Material Waste
High precision molds minimize the amount of material wasted during production. This efficiency not only reduces costs but also supports environmentally sustainable manufacturing practices.
Lower Costs Over Time
Although the initial investment for precision molds may be higher, the long-term savings are significant. With better quality control, reduced rework, and increased efficiency, manufacturers can achieve a more favorable return on investment.
How to Choose the Right Precision Molds for Your Business
Selecting the right precision molds is crucial for optimizing manufacturing processes. Consider the following factors:
1. Material Compatibility
The material used to create the mold must be compatible with the products being manufactured. Ensure that the mold material can withstand the temperature and pressure conditions of the production process.
2. Design Specifications
Customize mold designs to meet the specific requirements of your products. This may include considering factors such as tolerances, finishes, and functionalities.
3. Manufacturing Quality
Choose suppliers who utilize advanced manufacturing techniques and quality control processes to ensure that the molds produced meet industry standards and your specific needs.
4. Longevity and Maintenance
Consider the durability of the molds and any maintenance requirements. Investing in high-quality molds can extend their lifespan and reduce the frequency of replacements.
The Future of Precision Molds in Metal Fabrication
The future of precision molds in the metal fabrication industry looks promising, with advancements in technology continuing to push the boundaries of what is possible. Here are some trends to watch:
1. Automation and Smart Manufacturing
As automation becomes more prevalent in manufacturing, precision molds equipped with smart technology will facilitate more accurate production processes, reducing human error and increasing efficiency.
2. Additive Manufacturing
The rise of 3D printing is influencing mold design and production. Additive manufacturing allows for the rapid prototyping of molds, which can lead to improved designs and faster iterations.
3. Sustainability Initiatives
With a growing emphasis on sustainability, the development of eco-friendly molds and materials is becoming increasingly important. Manufacturers will seek ways to produce with less resource consumption and waste.
Conclusion: Maximizing Business Efficiency with Precision Molds
In today's manufacturing landscape, the adoption of precision molds is not merely advantageous; it is essential for staying competitive. Businesses that invest in high-quality molds can expect enhanced product quality, reduced waste, and increased efficiency across their production lines. By understanding the applications, benefits, and future potential of precision molds, companies can harness this technology to foster growth and excellence in the metal fabrication industry.
For more information on how precision molds can benefit your business, visit deepmould.net and explore our expertise in metal fabrication.