Injection Molding Tooling: Mastering the Art of Precision in Metal Fabrication
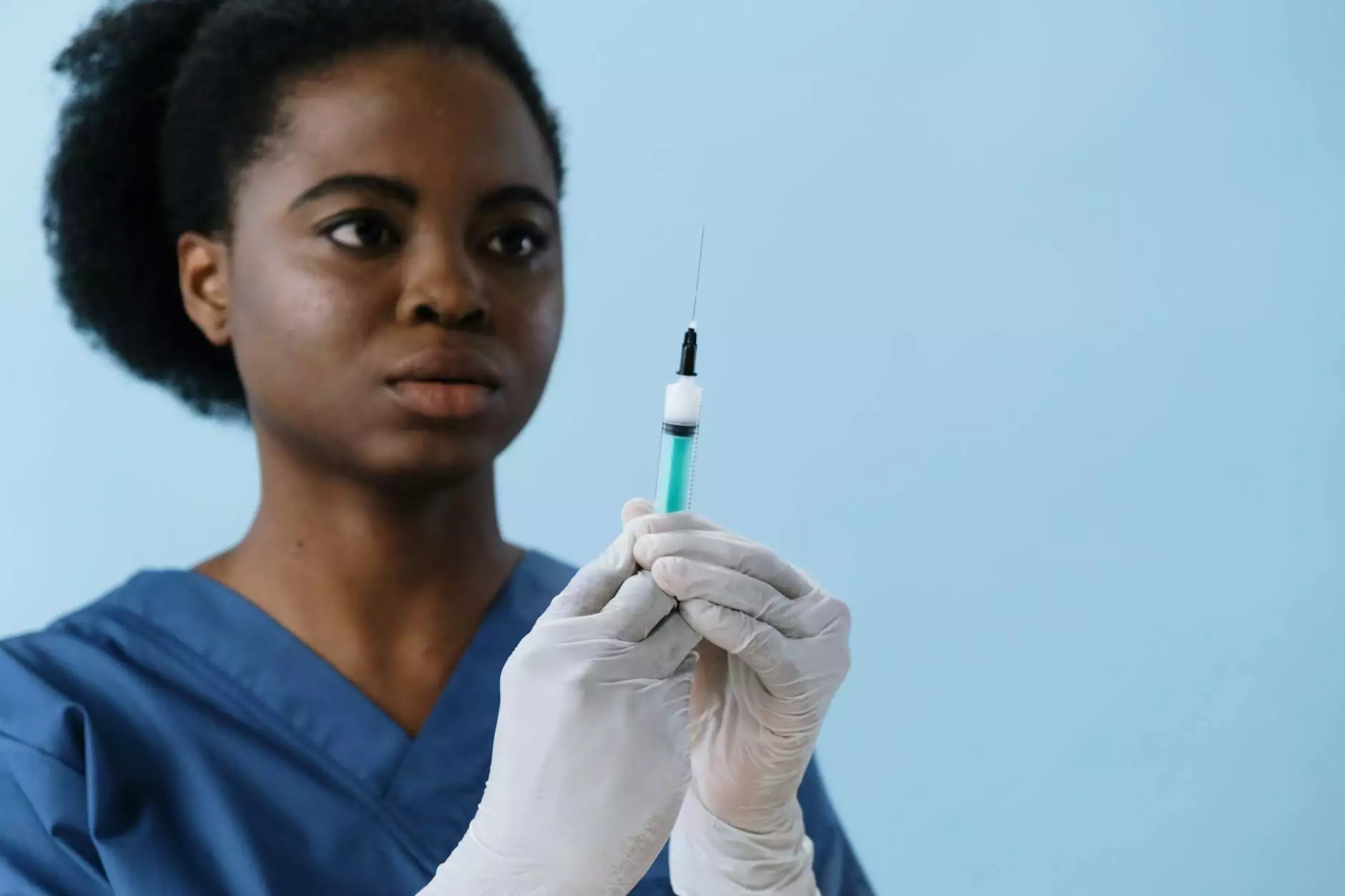
Injection molding tooling is at the core of modern manufacturing processes, particularly in the realm of metal fabrication. As industries evolve and consumer demands become ever more precise, understanding and leveraging effective injection molding techniques is essential for any metal fabricator aiming to stay ahead of the competition. In this comprehensive guide, we will explore various aspects of injection molding tooling, its importance, benefits, and how it can significantly enhance your business.
What is Injection Molding Tooling?
Injection molding tooling refers to the process of creating molds that are used in the injection molding process. This method involves injecting molten material into a mold to create specific shapes and parts, which are fundamental in manufacturing.
The Injection Molding Process
To understand injection molding tooling, let us break down the injection molding process:
- Material Selection: Choosing the right materials is crucial. Common materials include various types of plastics and metals.
- Mold Design: The design of the mold must accommodate the desired design specifications, ensuring optimal flow and cooling.
- Heating and Injection: The selected material is heated until it becomes molten, followed by injection into the mold under high pressure.
- Cooling: Once the material is injected, it cools and solidifies into the desired shape.
- Demolding: The final step involves removing the completed parts from the mold.
Importance of Injection Molding Tooling in Metal Fabrication
Injection molding tooling is vital for several reasons:
- Precision and Consistency: Proper tooling ensures that products are manufactured to exact specifications consistently.
- Cost Efficiency: High-quality molds reduce production costs through fewer defects and lower material waste.
- Customization: Injection molds can be designed to create a variety of shapes and sizes, accommodating a wide range of customer needs.
- Scalability: As demand increases, efficient tooling can support larger production runs without significant additional costs.
Types of Injection Molding Tooling
In the industry, several types of injection molding tools are commonly used. Each type serves specific purposes and applications:
1. Single Cavity Molds
These molds produce one part at a time, making them ideal for low-volume production or prototypes.
2. Multi-Cavity Molds
Designed to produce multiple identical parts in a single cycle, multi-cavity molds are perfect for large production runs.
3. Family Molds
These molds can produce different parts in one cycle, which is advantageous for products requiring various components that fit together.
4. Insert Molds
Insert molds use pre-made pieces—often metal—within the cavity, allowing for unique characteristics in the final product while maintaining strength.
5. Hot Runner Molds
A hot runner system keeps the material in a fluid state within the runners leading to the cavities, significantly reducing waste and improving cycle times.
Key Benefits of Using Quality Injection Molding Tooling
Investing in quality injection molding tooling comes with numerous benefits:
- Enhanced Product Quality: High-quality molds produce superior end products with fewer discrepancies and better finish.
- Reduced Lead Time: Efficient tooling reduces the lead time between design and production, helping businesses meet customer demands promptly.
- Lower Maintenance Costs: Durable molds require less frequent maintenance, further securing your investment and improving profitability.
- Eco-Friendliness: High-quality molds support sustainable manufacturing practices by minimizing waste and utilizing recycling options.
Best Practices for Injection Molding Tooling
To optimize the use of injection molding tooling, consider the following best practices:
1. Collaborate with Experienced Tool Makers
Partnering with skilled tool makers ensures that the molds are designed to accommodate both your product specifications and production requirements effectively.
2. Invest in Quality Materials
Utilizing high-grade materials in the mold production will increase longevity and performance. Stainless steel, for instance, is a popular choice for durable molds.
3. Regular Maintenance and Inspection
Conducting routine inspections and maintenance on your molds helps to identify any potential issues before they become significant problems, enhancing mold life.
4. Optimize Production Techniques
Stay updated with the latest production techniques and technologies in injection molding to improve efficiency and product quality.
5. Utilize Simulation Software
Employ simulation software during the design phase to anticipate and resolve issues before physical production begins, significantly reducing errors.
Common Challenges in Injection Molding Tooling
While injection molding tooling offers many advantages, challenges can arise:
1. High Initial Costs
Quality molds require considerable upfront investment, which can be a barrier for smaller manufacturing businesses.
2. Design Limitations
Adapting designs due to tooling constraints can hinder creativity and innovation in product development.
3. Maintenance and Downtime
Mold maintenance is essential but can result in unexpected downtime, impacting production schedules.
Integrating Injection Molding Tooling with Your Business
To integrate injection molding tooling effectively into your metal fabrication business, consider the following strategies:
1. Comprehensive Training Programs
Invest in training your workforce on the latest tooling techniques and best practices to maximize efficiency and effectiveness in production.
2. Continuous Research and Development
Encourage a culture of innovation within the company. Staying abreast of industry trends and technologies can give your business a competitive edge.
3. Customer Collaboration
Work closely with clients to fully understand their needs, providing them with tailored solutions that incorporate advanced injection molding tooling.
Future Trends in Injection Molding Tooling
As technology progresses, the injection molding industry is witnessing notable trends:
- Smart Manufacturing: The integration of IoT (Internet of Things) technologies to monitor and optimize the injection molding process in real-time.
- 3D Printing: The use of 3D printing to produce certain components of the molds, allowing for rapid prototyping and customized solutions.
- Sustainable Practices: An increasing focus on eco-friendly materials and practices to meet growing environmental standards and consumer preferences.
Conclusion: Embrace Injection Molding Tooling for Success
Injection molding tooling is not just a manufacturing responsibility; it is an integral part of strategic business advancement in the metal fabrication industry. By understanding its importance, utilizing best practices, and staying informed about innovations, businesses can capitalize on the numerous benefits it offers. Investing in quality injection molding tooling can position you as a leader in the industry, capable of delivering high-quality, precision-engineered products that meet and exceed customer expectations.
As you consider the future of your metal fabrication business, embrace the potential of injection molding tooling. With the right strategies and practices in place, you can enhance productivity, foster innovation, and ensure long-term success.