CNC Precision Machining: Revolutionizing the Metal Fabrication Industry
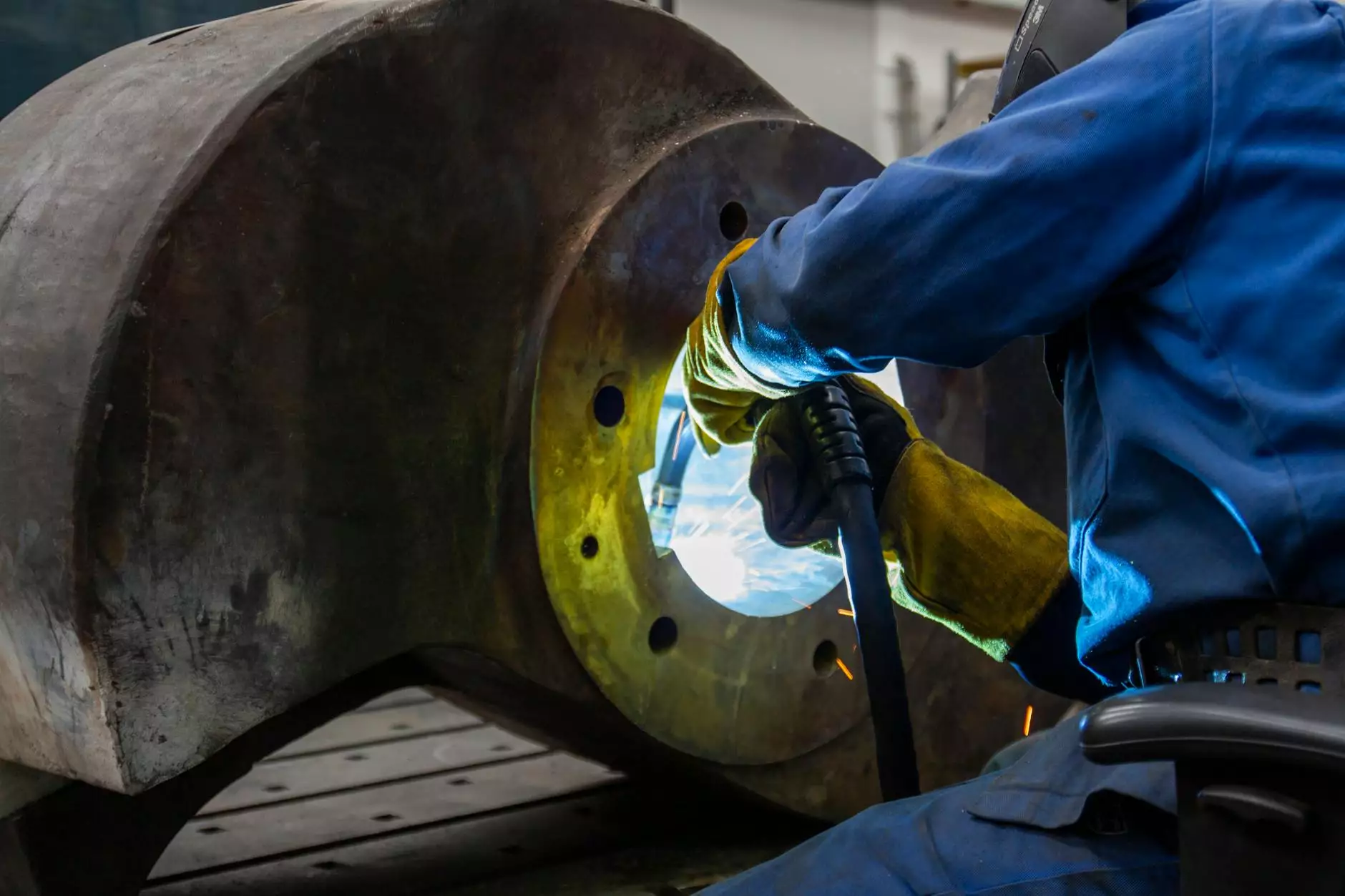
CNC precision machining has emerged as a pivotal factor in the evolution of the manufacturing and metal fabrication landscapes. With its ability to produce intricate parts with low tolerances, this technology has set a new standard for quality, efficiency, and reliability. In this comprehensive article, we dive into what CNC precision machining entails, its benefits, applications, and the innovative edge it brings to businesses like DeepMould.net.
What is CNC Precision Machining?
CNC stands for Computer Numerical Control, a method that employs computer software to control machine tools with remarkable precision. In the realm of metal fabricators, CNC precision machining refers to the automated process of machining components through the precise movement of tools and materials. This technology enables intricate designs that would be nearly impossible to achieve with manual machining methods.
The Mechanics Behind CNC Machining
The CNC machining process consists of the following steps:
- Design: Using CAD (Computer-Aided Design) software, engineers create detailed 3D models of the components.
- Programming: The CAD file is translated into G-code, a language that CNC machines understand to perform specific tasks.
- Setup: The machine is set up with the required tools, materials, and specifications based on the G-code.
- Machining: The CNC machine precisely executes the machining operations, including cutting, drilling, milling, and grinding.
- Finishing: Post-machining processes like polishing or coating may follow to enhance the final product's surface finish.
Benefits of CNC Precision Machining
There are numerous advantages to utilizing cnc precision machining in manufacturing:
- High Precision: CNC machining offers exceptional accuracy, making it ideal for producing components with intricate geometries and tight tolerances.
- Consistency: Automated processes ensure that every part produced is identical, significantly reducing the risk of human error.
- Efficiency: CNC machines can operate continuously and often faster than manual processes, resulting in increased production rates.
- Versatility: CNC machining can work with a wide range of materials, including metals, plastics, and composites.
- Cost-Effectiveness: Over time, CNC machining leads to lower production costs by minimizing waste and reducing the need for skilled labor.
Applications of CNC Precision Machining
The applications of CNC precision machining span a variety of industries, such as:
Aerospace
CNC machining is critical in the aerospace sector, where components must adhere to strict safety regulations. Parts like turbine blades and structural components are machined to exact specifications for optimal performance.
Automotive
The automotive industry leverages CNC precision machining to produce engine blocks, custom gears, and more, ensuring that every component meets rigorous standards for safety and performance.
Medical Devices
CNC machinery is used to manufacture high-precision components essential in medical devices, such as surgical instruments and implants, where failure is not an option.
Defense
With stringent standards for reliability, CNC precision machining is vital in creating parts for military equipment, firearms, and other defense systems.
Electronics
The electronics industry utilizes CNC machining for parts like housings and connectors, where precision can significantly affect functionality.
Choosing the Right CNC Precision Machining Service
When selecting a CNC precision machining provider, consider the following criteria:
- Experience: Look for companies with proven experience in your specific industry.
- Capabilities: Ensure the provider has the necessary machines and technology to meet your needs, including advanced capabilities like 5-axis machining.
- Quality Assurance: Investigate the measures in place for quality control, like ISO certifications or similar standards.
- Turnaround Time: Assess lead times and scheduling flexibility to ensure timely delivery of your parts.
- Customer Support: Strong communication and support throughout the project are crucial for your satisfaction.
The Future of CNC Precision Machining
The future of cnc precision machining looks promising, with ongoing advancements expected to drive the industry forward:
Automation and AI
Artificial Intelligence (AI) is set to revolutionize CNC machining by optimizing production schedules, improving workflow, and enhancing predictive maintenance.
Internet of Things (IoT)
Integrating IoT technology into CNC machines can provide real-time monitoring and analytics, allowing for better decision-making and enhanced efficiency.
Sustainable Practices
As sustainability becomes increasingly crucial, CNC machining is likely to evolve toward greener practices, focusing on reducing waste and energy consumption.
Conclusion
In summary, cnc precision machining stands at the forefront of modern manufacturing, significantly impacting sectors ranging from aerospace to electronics. By implementing advanced CNC technologies, businesses can enhance their operational efficiency, reduce costs, and improve product quality. As industries evolve, CNC precision machining will undoubtedly adapt, incorporating innovative trends and technologies, ensuring it remains essential in the metal fabrication industry. For more information and to explore our services, visit DeepMould.net.